Error Recovery Strategies in CAD Workflows
UX Case Study | Design System | User Research
Dassault Systèmes, 2023
Case Study on Understanding User Requirements and Enhancing User Experience in Troubleshooting Scenarios within CAD Modeling Workflows
Concept Story
The table lamp story

Meet Sam, After months of planning, Sam finally decided to start a DIY project: Building a custom table lamp.

To bring the idea to life, Sam used CAD software to design a 3D model, simulating mechanisms and electrical wiring.

Some components for the model were sourced from Alex, an external supplier.
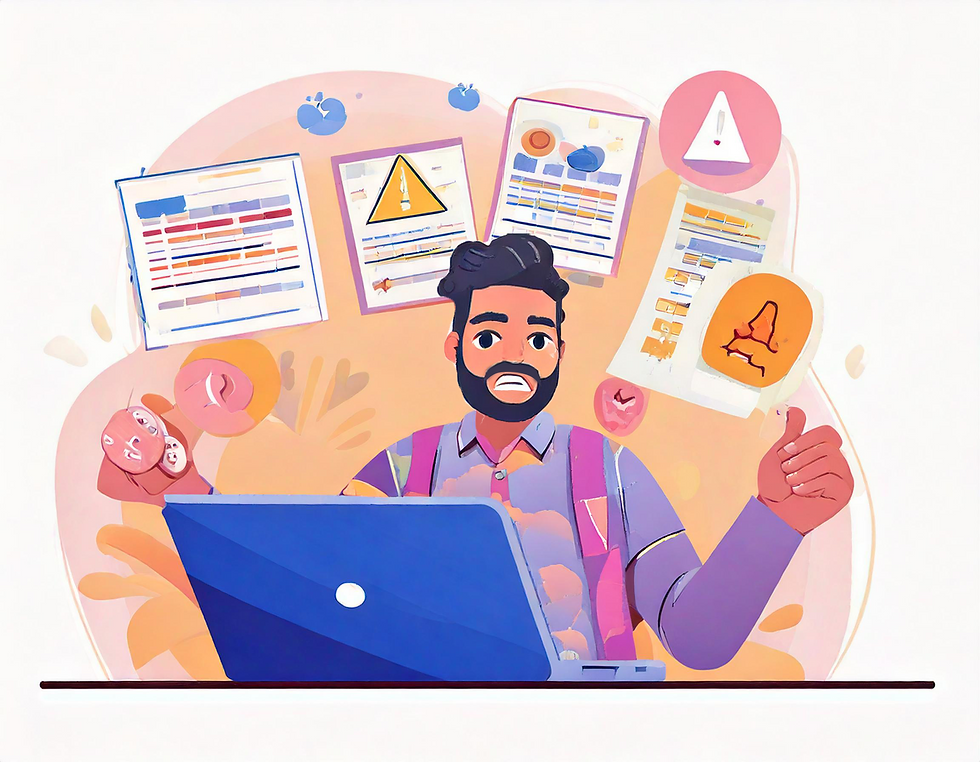
Things seemed to be going smoothly until Sam began assembling the parts in the CAD software. That’s when issues emerged—several components from Alex didn’t align properly.

Determined to fix the problem, Sam manually adjusted dimensions, hoping to correct the misalignment.Instead, the changes triggered a series of errors and warnings in the CAD software’s design history.

Sam tried to decipher the messages, error and warning highlights but they were too vague to provide clear guidance, leaving Sam stuck and frustrated.
This wasn’t just Sam’s problem—it’s a common challenge in CAD workflows.
The issue stems from reference-based modeling, where even small misalignments can snowball into complex errors.As models grow more intricate, identifying and fixing issues becomes increasingly difficult for users.
Background
Designing physical products often requires multiple iterations, making CAD models crucial for testing ideas and refining designs.
'xApps', SolidWorks web application for CAD modeling, plays a central role in this process.
However, given its rich features, it’s important to ensure users can easily track system status and understand ongoing changes.
My Role
As a UX designer, my goal was to tackle this head-on.
I worked to understand user pain points, map the underlying issues, and design feedback mechanisms that appear at the right moments.
By providing clear and actionable guidance, I aimed to make error recovery in CAD smoother and less frustrating.
Team
UX Designer(3) | User Researcher(1) |
Documentation (1)
Deliverables
Research | Design | Usability Testing | Dev Handoff
Duration
5 Months
Challenges
Feedback can take various forms, such as a warning message alerting the user that a dimension exceeds the manufacturable limit of the machine they will use to produce the modeled part.This information can be shown to the user in different ways, guide or alert to make the necessary actions.

Legacy Issue
Legacy users rely on a metal model based on the original desktop application, which creates discoverability issues despite the new workflow being designed to optimize task efficiency.
Inconsistent Feedback
Over four years of development, hundreds of feedback behaviors were created across projects, including messages, graphical indicators, and model signifiers like color changes or warnings. The lack of early guidelines led to inconsistency in applying these feedback methods across different scenarios.
Timeline
'The majority of the effort for this project focused on the discovery phase, aiming to understand what would help users recover from errors, with solutions varying based on the complexity of the issues.'
- Statement from final presentation
Research and
Discovery
Exploring how users handle errors in CAD workflows.
5 Weeks
Framing the
Challenge
Defining pain points and user needs.
2 Weeks
Crafting
Solutions
Designing improved feedback systems.
4 Weeks
Prototyping and Validating
Prototyping and testing with users.
4 Weeks


The process involved running a test scenario intentionally designed to fail, aiming to observe how users recover from errors and warning states within the existing framework.
One-on-one sessions captured detailed insights into the workflow, while breakout sessions encouraged feedback through live questionnaires and group discussions between sessions.
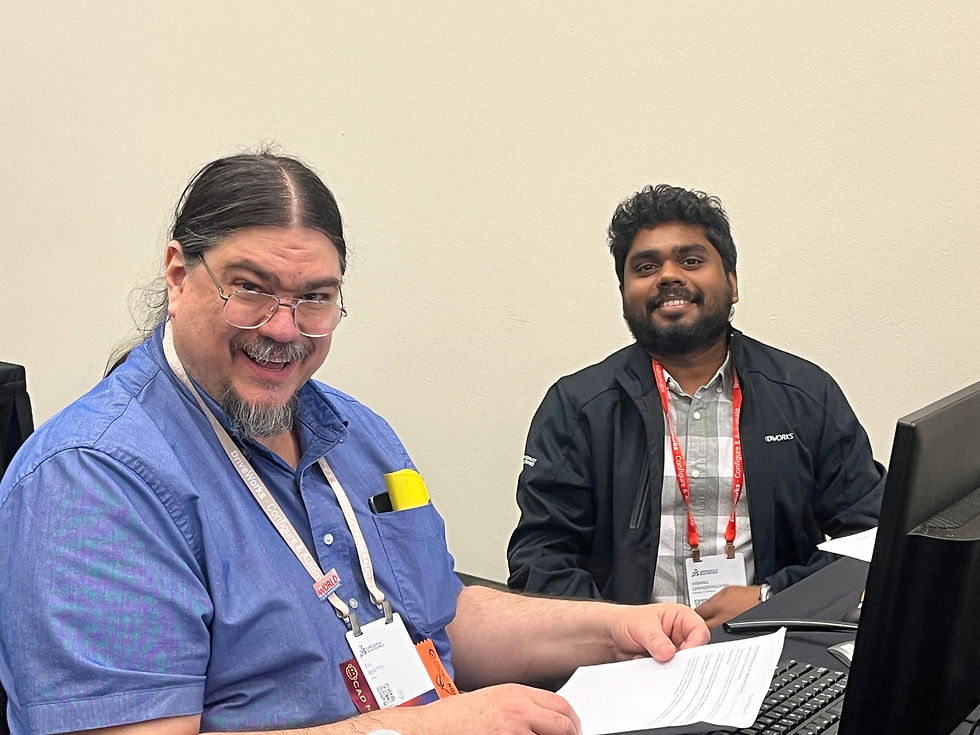

1-1 User testing,
3D Experience World 2024, Boston, USA
Breakout Session,
3D Experience World 2024, Boston, USA
#Observation 1
Inconsistent use of different formats of messaging
Users were unsure which specific change caused the model failure or the sequence in which failed items needed to be addressed to resolve the entire model effectively.
"Its frustrating not knowing where to start the fixing"



#Observation 2
Feedback messages not helping users to fix the problem.
Currently, the messages only explain what went wrong, avoiding additional details to prevent overwhelming the user.
However, this minimal approach isn’t helping users effectively resolve the issues they face.
#Observation 3
We found a popular sequence for fixing issues
Users preferred addressing issues in a top-down approach, expecting that fixing problems at higher levels would resolve multiple downstream issues in the sequence from the first to the last created item.



#Observation 4
Collaboration becomes a nightmare
The person who observes errors and warnings during their own actions might understand the cause based on their context.
However, when a second person inherits the model, they rely on UI messages and visual cues to figure out what went wrong.
This becomes particularly challenging with complex models, where errors or warnings in the design history are easily overlooked, increasing the likelihood of missing crucial information.
What went wrong?
Problem Breakdown
Error messages lack actionable guidance, leaving users unsure how to fix issues. Secondary users, without context, find it harder to identify causes or navigate design history in complex models.
Additionally, the system doesn’t align with users’ mental models, as they expect top-level fixes to resolve downstream issues. This mismatch adds to confusion and inefficiency.
Key Insights
The research insights were categorized into three primary usability issue themes.
-
Clear visual cues helped users recognize straightforward issues without needing text.
-
Combining visuals (e.g., red highlights) with concise text boosted usability for diverse user preferences.
Understanding System Status
1
-
Immediate feedback like pop-ups worked better than delayed or subtle indicators.
-
Consistent feedback elements (e.g., uniform error colors) enhanced recognition and understanding.
Discoverability of Feedback
2
-
Actionable, specific messages aided error resolution.
-
Overlapping errors in complex models overwhelmed users, hindering recovery.
-
Lack of context in shared workflows complicated collaborative troubleshooting.
User Recovery from Errors
3
Key Problems to Solve
-
Users find feedback messages unclear, hindering issue resolution.
-
The disconnect arises when messages don’t align with users' mental models or expected resolution processes.
Key Problems to Solve
-
Inconsistent feedback messages confuse users, hindering issue identification and resolution.
-
Errors are displayed based on criticality, but varying situations require different feedback, highlighting the need for a unified resolution system.
Key Problems to Solve
-
Users face unclear guidance in resolving errors, especially in collaborative workflows and complex models.
-
Dynamic, scenario-based guidelines are needed to define feedback behavior for better clarity and usability.
Brainstorming & Prioritisation
Leave no stone unturned.
We explored all potential solutions to the problems we identified.
The next step was to map these solutions on an effort and impact chart, which helped us prioritize and focus on the most valuable ideas to work on.

We developed prototypes for some of these concepts, positioning them as MVPs for inclusion in a decision matrix. My primary goal was to reduce complexity and create an intuitive experience, particularly for novice CAD users.

We developed a decision tree to assist stakeholders, including UX designers, product owners, and development teams, in creating consistent and effective feedback messaging throughout the CAD workflow.
Benefits for Stakeholders: The decision tree provided clear guidance on placing the right messages—whether during active commands, dialog panels, or pre-emptive warnings—ensuring contextual relevance and consistency across scenarios.
Impact on End Users: Benefit from improved feedback messaging. Clear, timely, and consistent messages guide users effectively, reducing confusion, preventing errors, and enhancing the overall CAD experience.
Pros
-
Ensured consistent messaging.
-
Simplified decision-making.
-
Introduced a new message format.
Cons
-
Stakeholders found it difficult to use.
-
Full engagement and success were not achieved.
Exploration 1:
Decision Tree for Stakeholders
Design System (Selected)

We explored visual indicators in the graphic area to highlight entities involved in conflicts, using flag components or signifiers like color-coded highlights.
Key Features:
-
Flags visually connect child entities to their parent conflicts.
-
Highlights indicate the resolution sequence, guiding users step-by-step.
Pros
-
Immediate visual feedback makes conflicts easier to spot and prioritize.
-
Intuitive association between parent and child entities improves resolution flow.
Cons
-
Added screen elements could clutter the workspace.
-
Complex models might overwhelm users with too many visual cues.
-
Developing this solution required creating new UI elements beyond the existing design system. Additionally, implementing a new data model and logic significantly increased development and QA costs.
Exploration 2:
Visual Indicators for Impacted Model Entities
New Feature (Rejected)
_edited.jpg)
A single source of truth for all issues relevant to the user in the CAD workflow.
A feedback system , offering users real-time updates on errors or conflicts in their CAD models. This feature aimed to improve clarity by pinpointing problematic components or actions.
A data grid was introduced to present error/warning details within the workflow, streamlining troubleshooting and enabling seamless adjustments in real time.
Pros
-
Minimized the risk of overlooking errors or warnings, significantly reducing human error.
-
Streamlined decision-making by presenting users with structured insights.
Cons
-
Technical limitations: The system couldn't dynamically update the data grid as per specifications, requiring users to manually refresh it.
-
Impact on usability: This workaround made the experience less intuitive and often caused confusion by displaying outdated information.
Exploration 3:
Error and Warning Manager
New Feature (Selected)
After stakeholder discussions and evaluating what would provide the most value to users,
We decided to focus on developing an 'Error and Warning Manager.'
Error and Warning Manager
Goal
This feature enhances issue resolution, improves CAD workflow efficiency, and promotes seamless collaboration, driving measurable KPI improvements.
Key Features
-
Real-time feedback on CAD errors and conflicts.
-
Data grid for error/warning details and real-time adjustments.
-
Direct editing from the command to fix issues with items.
What does the existing IA say?
There was no well-defined error recovery strategies in the workflow, leaving the efficiency of resolution tasks entirely dependent on user decisions and interpretations.
Analysis revealed a pattern that users often rely on manually scrolling through modeling history to troubleshoot CAD issues, which is inefficient and prone to human errors.

Problem
The tedious task of endlessly scrolling through the 'design history' to identify issues, while simultaneously trying to understand their causes and resolutions, often overwhelms users, leading them to abandon the task altogether
Solution
Multiple iterations and technical feasibility checks were conducted to arrive at an acceptable solution for this problem.
One of the proposed solutions was a data grid that lists the issues within the model.


Problem
After identifying what went wrong, the next challenge was resolving the issues, which proved to be just as tedious.
Users had to individually select each affected entity, interpret the feedback messages or visual indicators, edit the features one by one, and address the issues.
In some cases, this process could lead to the failure of linked entities, further complicating the task.
Solution
From the insights from usability testing we found a pattern on how the users prefered to resolve the issues and reasoning behind that
Problem
Users struggle to find relevant issues and prioritize them during CAD modeling, leading to wasted time and confusion.
Solution
Filters show only component-specific issues and prioritize them by complexity, streamlining the process.


Problem
The UI copy used in various message formats, such as errors, warnings, or informational messages, did not always effectively guide users—especially novice users—on how to resolve the issues.
Solution
We improved UI messaging by focusing on clarity, timing, and discoverability.
My UX role involved designing message formats tailored to the criticality of each situation, ensuring users received the right information without feeling overwhelmed. User testing validated that the messages were clear, actionable, and effective.
How Error and Warning Manager changes the IA/Workflow ?
A defined error recovery strategy improved task resolution efficiency.
Users no longer rely on manual history scrolling, with real-time feedback and a data grid streamlining issue resolution.

When an industrial CAD designer models a product, they utilize various tools within the application for different manufacturing processes. Our focus is on creating a single source of truth that the user can rely on throughout the entire modeling process.
The below workflow is a short glimpse from one of the prototypes tested.


Evaluation
This project was one of the most extensive I have worked on, given the volume of information handled and its significance, which ultimately shaped the design system.
The final version was made available for hands-on use during beta events in late 2024 and became a popular highlight in the 'What's New?' session at the product showcase.
Measuring Improvements
The usability testing workflow remained the same, but with the integration of the Error and Warning manager.
The test criteria focused on users' ability to discover, diagnose, and fix issues. Success was measured by the time taken and the accuracy of the diagnostics.
User feedback on intuitiveness
Even though user assistance support was available and users were made aware of it, they found the workflow intuitive regardless.
During testing, they were able to understand and execute the command effectively, appreciating the clear and logical relationship between actions and outcomes.
Dynamic Update fail and discoverability issue
The data grid holds features and components with errors or warnings. When users fix issues through direct editing from the Error & Warning Manager, the current data model has a limitation—it cannot update the data grid instantly, causing confusion.
A temporary fix was added to the design until the limitation is resolved.
Future Scope
This project was seen as a significant step towards full automation. By leveraging machine learning, it aims to implement a status monitoring logic running in the CAD background, which will assist users in error prevention and help them fix issues.
"I like how everything is shown upfront, with simple workflows within it."
Eric _
Industrial Designer
Takeaways
Improving CAD workflows required deep user research, iterative design, and cross-functional collaboration. By identifying pain points and refining error-handling mechanisms, I was able to enhance user efficiency and streamline interactions.
Highlights
-
Identified Usability Issues – 1-1 usability tests uncovered inefficiencies, workarounds, and user frustrations.
-
Optimized Error Handling – Integrated a feedback system to improve error resolution and guide users effectively.
-
User-Centered Design – Ensured solutions were based on real user behaviors while maintaining technical feasibility.
-
Cross-Functional Collaboration – Worked closely with engineers and product teams to align design with business and technical goals.
-
Iterative Improvements – Adapted to evolving requirements, addressing user challenges incrementally for a smoother workflow.
-
Future Application – These insights will help me design more intuitive and efficient CAD experiences.